1) Color
- Yellow becomes greenish yellow
- White becomes dirty white
Causes
- Over heating of material
- Mixing of old and new material;
Solution
- Control heating temperature between 180 – 200°C.
- Do not melt the material inside the Preheater very long [Not more than 3 Hours]
- Empty the Preheater content and put new material if color change occurs.

2) Peeling off due to less adhesion
Causes
- Moisture, Grease & Oil Stuck on the Surface
- Too dry prime coat
Solution
- Clean road surface from dust, moisture, grease and oil properly.
- Wait for the right timing between the wetness and the dryness of prime coat before applying the Thermoplastic. Stick finger tip to the prime coat surface, if it’s almost dry but still sticks to finger tip, then that’s the best time to apply the melted Thermoplastic
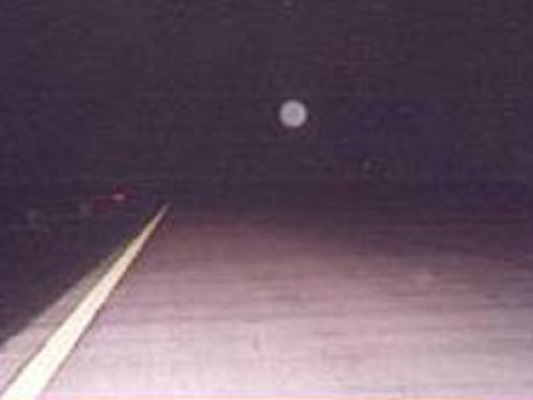
3) Poor reflectance at night and wet road condition
Causes
- Uneven or insufficient dispersion of glass beads
- Weak adhesion of glass beads on marking strips
Solution
- Adjust the dispersing rate of the glass beads dispenser.
- Check the sufficiency of the glass beads in the glass beads box.
- Try to install the chain driven glass bead dispenser for uniform sufficient dispensing of glass beads.
4) Hollow craters on strip surface
Causes
- Wet prime coat upon application of melted Thermoplastic.
- Wrong viscosity of the molten thermoplastic causing uneven amount
- Road surface temperature is below 10°C
Solution
- Melt the Thermoplastic to the required temperature.
- Adjust screeding shoe opening to suit viscosity
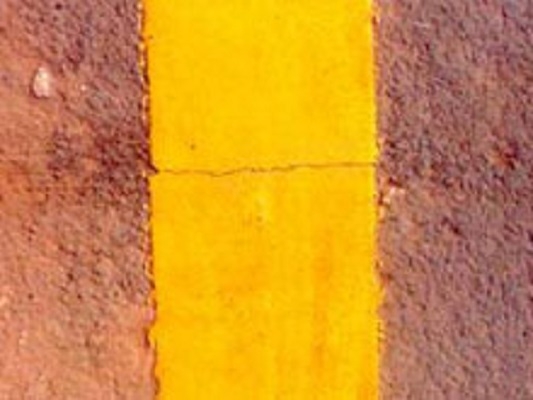
5) Cracks reaching the road surface
Causes
- Cracks on some portion of the road surface.
- Thermoplastic is too hard and cannot cope with the softer asphalt road surface.
- Uneven thickness causing some portion to crack on heavy traffic
Solution
- Adjust the viscosity of the Thermoplastic to increase its flexibility by controlling the temperature using thermometer.
- Calibrate the thermometer at regular intervals.
- Apply uniformly and evenly.
- Apply drop on Glass beads to cover small cracks on the line film of Thermoplastic.
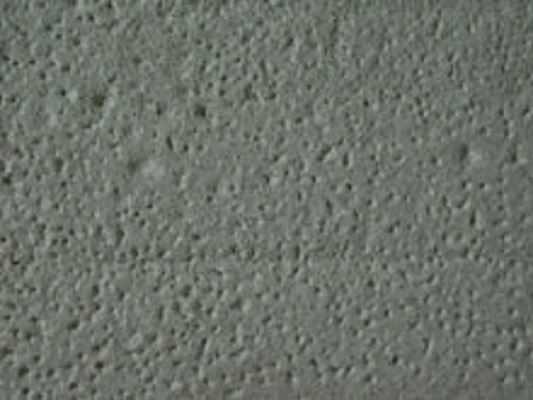
6) Tiny holes on thermoplastic strips
Causes
- High melting and applying temperature
- Expanded air inside open void of the road break through the wet Thermoplastic.
- Road surface temperature is below 10°C.
Solution
- Lower the temperature of the Thermoplastic.
- Apply drop on Glass beads to cover pin holes and other line defects.
- Use road heater equipment to warm the road surface before applying the melted Thermoplastic if the road surface temperature is below 10°C.
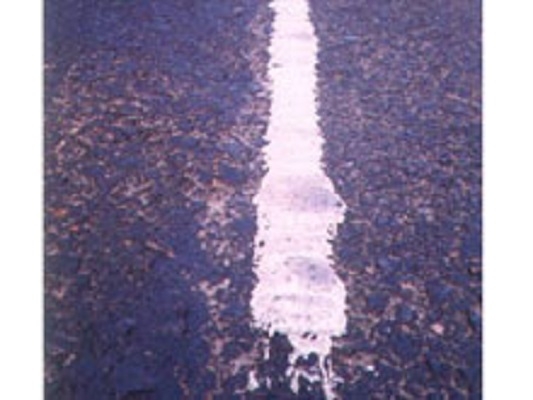
7) Scattering of excess thermoplastic material at sides
Causes
- Over melting temperature than the required standard temperature.
Solution
- Reach the required standard melting temperature and maintain this temperature then apply the melted Thermoplastic
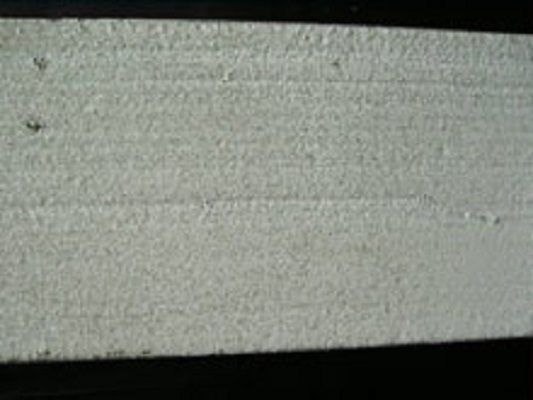
8) Open, deep and long groves on surface of thermoplastic strips
Causes
- Screeding shoe discharge point is choked with hardened Thermoplastic solids and foreign solid particles
Solution
- Check the filter sieve.
- Get rid of the foreign matters like small solid particles.
- Clean and sharpen the screeding shoe blade.
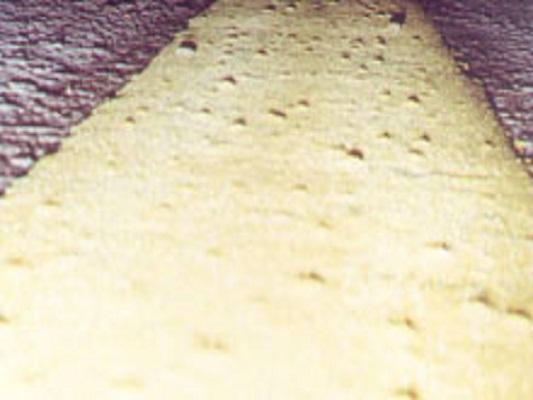
9) Tiny bubbles popping up on surface of thermoplastic strips
Causes
- Insolated moisture evaporates & expands inside wet concrete.
- Evaporation and expansion of moisture under road surface.
- Solvent evaporates from wet prime coat.
- Road surface temperature is lower than 10°C.
- High melting and application temperature.
Solution
- Apply Thermoplastic if the concrete is properly aged (wait for 2 weeks or more).
- Calibrate the thermometer at regular intervals.
- Allow moisture to dry completely (new asphalt wait for 1 week or more).
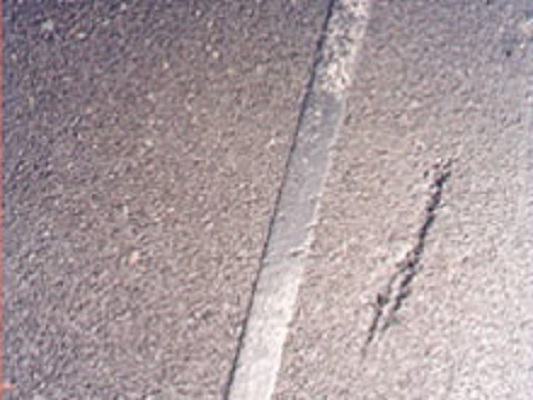
10) Black spots on surface of thermoplastic strips
Causes
- New asphalt road surface not properly aged.
Solution
- Wait for one week after workup of new bitumen surface. Let traffic move for some time before applying thermoplastic.

11) Small solid particles found in melted thermoplastic material and thermoplastic strip after application
Causes
- Wrong melting temperature.
- No strainer used while transferring melted material from preheater to applicator machine tank.
- Over loading of preheater more than 80% of its capacity and non-uniform agitation of material in preheater.
Solution
- Load materials 80% of the preheater tank capacity and stir constantly while melting and before application.
- Use strainer to transfer melted materials to the applicator machine.
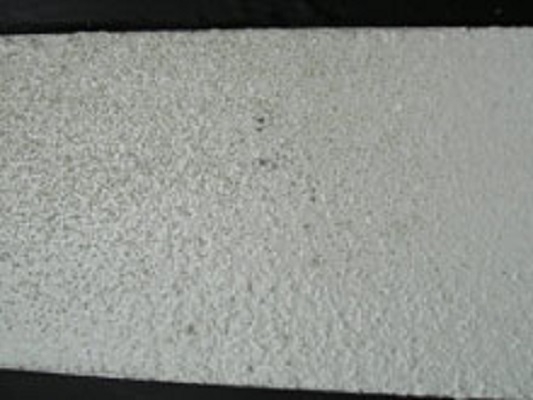
12)Wavy and irregular edges
Causes
- Flow-out of material. Edge is not well defined, caused by material being too hot or too liquid, application pressure being too high, screed gate open too wide, and/or surface being too uneven.
Solution
- Make sure temperature is 180 – 200°C and decrease application speed on rough surface.
- Make sure that the thickness is not more than specified thickness.
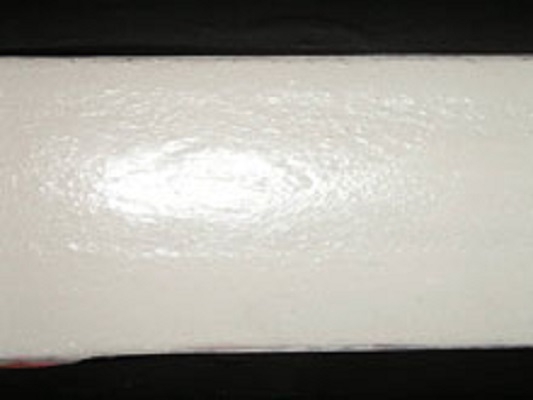
13) Smooth shiny glossy thermoplastic strips
Causes
- No Glass Beads, resulting in no retro-reflectivity caused by malfunctioning gun or Glass Beads sinking too deep.
- Drop-on Glass Beads sunk too low, resulting in lower retro-reflectivity, caused by material being too hot.
- Glass Beads not adhered well, will wear off quickly, caused by too cold material or bead gun being positioned too far from application point.
Solution
- Repair Glass Beads Dispenser. Align glass beads dispenser closer to the screed.
- Calibrate the thermometer at regular intervals.
- Maintain applcaton temperature between 180 – 200°C.